Home
Profile
Product Range
Industries
Infrastructure
Our Quality
Custom Manufacturing
Network
Contact Us
Send Enquiry
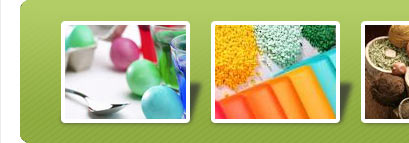
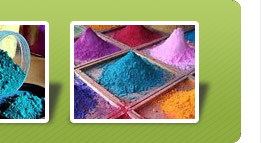
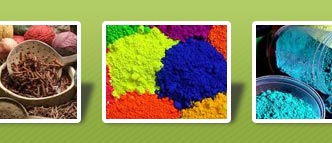
Dye House
Dye House is a building in which dyeing is carried on.
For improving quality and fast turn arounds, there is a need of fully
integrated dye house network that comprises of a vast range of automated
system components properly synchronized to each other. With the proper
integration of dyeing equipment into a sound organized network, it is quite
obvious that the dyehouses can give away its valuable resources very
cheaply.
A typical Dye house network should be equipped with the machines that are
capable of performing a number of operations like dyeing, heat setting,
compacting, stentering, hydro-extraction, brushing and washing etc. Another
vital task is the control of the system. Although every single device from
the color kitchen to dyeing machines these days are PC-controlled, however
modern dye houses prefer to employ a Dye house automation system.
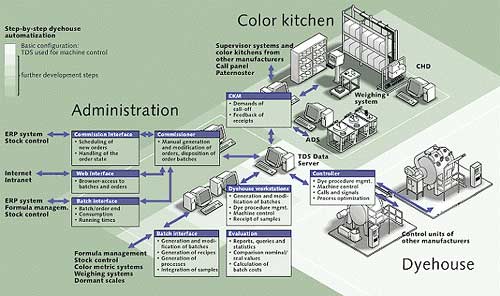
Dye house automation system ensures that the machines are able to
synchronize with each other and can optimise their capacities. Apart from
this the automation system facilitates linking of the order management with
the necessary machine control units. This helps to complete a fully
integrated dye house network. The diagram that follows next gives a perfect
example of Dye house that is complete in every respect. Most modern dye
houses are today following the concept of totally networked Dye House.
Benchmarks of a Dye House
A perfect dye house should meet the following
criteria, that are given below:
A perfect dye house should meet the following criteria, that are given
below: Computer aided Dyeing system- By implementing a Computer aided Dyeing
system it has been possible to cut down on both costs and time. For example
it has been found that by using the system there has been reduction in the
acrylic dyeing batch time by at least 30 percent.
Modern laboratories- New formulas are first tried in the lab before
implementing in production. If there is closer liquor ratio agreement
between the production and laboratory, better would be the final result.
Package preparation- Latest stainless steel spacer should be used for
holding the shape of package ends. This allows for smooth unwinding. Though
backwinding to paper cones along with intermediate lubrication is more in
vogue, but that costs money and time. Dyers must master new ways to bypass
the idea of backwinding.
Package handling- Increasingly the dye houses are insisting on the
technology of robotic package handling. Use of Robotics demands uniformity.
Robots need the packages to be placed in a specific location.
Quality- In today's fiercely competitive market, if a manufacturer doesn't
have a consistent quality, probably they just can't stay put in business.
Therefore a manufacturer must insist on receiving only quality and genuine
products from suppliers. In fact adhering to different International quality
standards that has written down procedures and manuals is now more than just
a norm. There are now various information technology companies that are into
the field of operations management. If they are called for and allowed to
work on a program at a dye house and follows up it through the completion,
then a dye house will be equipped with a totally integrated data base
system. This will offer solutions in every sphere of operations like
manufacturing, production, financial, forecasting, planning, scheduling and
delivery.
Challenges of globalisation- Over the years the supply of material has
changed. Today suppliers are challenged from across globe with products of
superior quality, and low cost. For example yarn suppliers continues to
search for non-branded suppliers of polyester and acrylic for replacing more
costlier brand names. Today's mantra is innovate or perish.
Savings in energy- Saving in energy, chemicals and water is now vital for
survival of any dye house. Machine vendors are now constantly redesigning
dye machines that has the lowest liquid to goods ratio. For example a high
pressure dyeing machine consumes much less water for processing. The liquid
to goods ratio being 1:5 (i.e. to process 1 kilogram of fabric, five litres
of water are used) now compare this to traditional units that are fitted
with conventional winches whose water to liquid ratio is in the range of
1:15 or even sometimes 1:20. Survival for such dye houses is impossible.
Maintenance- It is a general tendency to view maintenance time as an
opportunity lost to manufacture dyed sales yarn. Preventive maintenance is
clearly less expensive than unscheduled halt and a spoiled dyeing.
Home
Profile
Product
Range
Industries
Infrastructure
Our
Quality
Custom
Manufacturing
Network
Contact
Us
Send
Enquiry