Home
Profile
Product Range
Industries
Infrastructure
Our Quality
Custom Manufacturing
Network
Contact Us
Send Enquiry
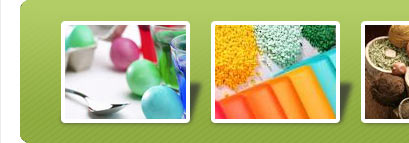
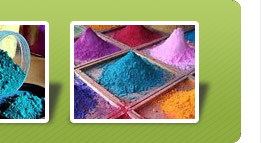
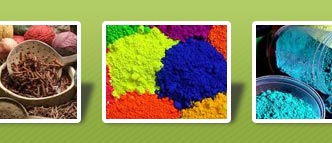
Dyeing Process
Dyeing is the process of adding color to textile products like fibers,
yarns, and fabrics. Dyeing is normally done in a special solution containing
dyes and particular chemical material..
The most widely publicised dyeing process is in the context of textile
dyeing, but now the dyeing process is used in a variety of industries like:
leather, plastics, paint, printing and many others.
Dyeing Process of Leather
The process of tanning and dying leather is
ancient. Primitive man was a society of hunters and gatherers who used
everything they caught, which meant that after an animal was eaten, its
carcass, hair, skin and organs needed to be used. Animal skins quickly
putrefy, so these people had to quickly discover a way to preserve them.
Adding color to cured animal skins - or simply put, dying leather - is a
part of the tanning process. The dying process is usually done in the third
and final stage of a tanning process, but is sometimes done in the second
stage, at the same time as the actual tanning. Tanning leather is necessary
to preserve an animal skin for use in making products like purses, jackets,
luggage and shoes. In ancient times, leather was used on everything from
battle armor to chariot wheels.
There is a lot of scope of experimenting with the dyes on the leather. You
can add designs, pictures or monograms on the leather, to make it look more
attractive. However, to achieve such results you need a lot of practice.
There are mainly two different types of leather, used for making leather
items. One is the aniline leather that shows the natural characteristics of
the hide. The other one is the nubuck leather, which is aniline leather that
has been brushed and polished to obtain the texture of a velvet. The steps
to dye leather have been given below:
Selecting the Right Dye- Choose the dye on the basis of the dyed
leather samples that are provided by the shop owners at the time of
purchase. This is because, most of the dyes, when applied on the leather,
give an altogether different color than what they seem when kept in a
bottle.
Preparing the Leather before Dyeing- In order to maintain its
natural color, leather surfaces are often coated with a protective covering.
If this coating is not removed from the leather, then you may find the
leather in a dull and mutilated condition after dyeing. Clean off coatings
or any other dirt present on the leather with the help of a leather
deglazer.
Application of Leather Dye- Spray water on the leather or apply it
with the help of a moistened sponge. Start applying the dye, when the
leather is evenly wet. While dyeing, try to keep your strokes long and to
ensure an even distribution of the color all over the surface of the
leather. It may happen that one coat of the dye may not give you the desired
shade. In that case, you have to apply more number of coats.
Drying Process- When the surface of the leather does not have a wet
look that means that the dye on the leather has dried up. On an average, it
takes almost one to two hours for the dyed leather to dry. To a great
extent, the drying time depends on the type of the leather to be dyed.
During this time, you need to flex the leather a number of times, in order
to loosen up its fibers. In this way, you can prevent the leather from
stiffening up.
Final Touch- Giving final touch to leather is most important. The
next step that follows drying, is buffing up the leather with the help of a
soft, clean cloth for removing the extra dye present on the leather. It also
helps the leather to get a polished look. Finally, you have to coat the dyed
leather with leather finish. Leather finishes are available in spray cans.
You can directly spray it on the leather surface or apply it with the help
of a wool dauber. The finish should spread on the surface evenly.
Inkjet Manufacturing Process
The manufacturing of inkjet process involves the
following:
- In the manufacturing process, only the best quality raw materials are
acceptable.
- A spanking clean room environment is a must.
- In filtration lies the key to a successful ink making process -
generally 0.2 to 0.4 micron filters reduce foreign material in ink.
Considerations in the manufacturing process
The following points are vital in the manufacturing of inkjet and needs to
be particularly taken care of:
- The ink ingredients must show stability this is important for
avoiding separation or sedimentation.
- Retention of samples are vital as color and purity of colorants along
with other ingredients can vary with different batches.
- Checking for any chemical reactions to cartridges is also essential.
- Material safety data sheets (MSDS) are also needed.
- 'Recipe' needs to be followed according to the specifications.
The diagram illustrates a typical dye based ink formulation
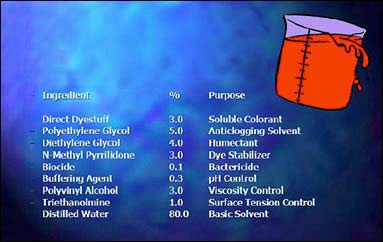
Textile Dyeing Process
Dyeing is a method which imparts beauty to the
textile by applying various colors and their shades on to a fabric. Dyeing
can be done at any stage of the manufacturing of textile- fiber, yarn,
fabric or a finished textile product including garments and apparels. The
property of color fastness depends upon two factors- selection of proper dye
according to the textile material to be dyed and selection of the method for
dyeing the fiber, yarn or fabric.
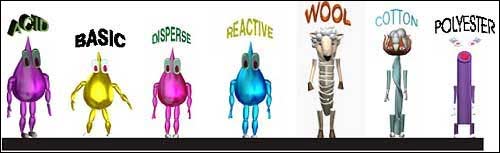
The following figures illustrate with process flow diagrams the whole
operation of finishing processes and how the dyeing process is a part and
parcel of the process of textile making.
Materials used in the Textile Dyeing Process
Materials that are used in textile dyeing process
include water, fibre, yarn or cloth. Further, these include a host of
process chemicals like:
- Acids, e.g. acetic, formic.
- Alkalis- NaOH, potassium hydroxide, sodium carbonate.
- Bleaches- Hydrogen peroxide, sodium hypo chlorite, sodium chlorite
etc.
- Dyes, for example direct, disperse, pigment, vat.
- Salts, e.g. NaCl.
- Size, e.g. PVA, starch.
- Stabilisers from sodium silicate, sodium nitrate also organic
stabilisers.
- Surfactants
- Auxiliary finishes, like fire retardant, softener
Methods of Textile Dyeing
Color is applied to fabric by different methods
of dyeing for different types of fiber and at different stages of the
textile production process. These methods include: Direct dyeing, Stock
dyeing, Top dyeing, Yarn dyeing, Piece dyeing, Solution pigmenting or dope
dyeing, Garment dyeing etc.
Textile materials are generally dyed using two processes. They are the
following:
- Batch Dyeing Process
- Continuous or Semi- Continuous Process
The following chart gives a comparison between batch dyeing and
continuous dyeing
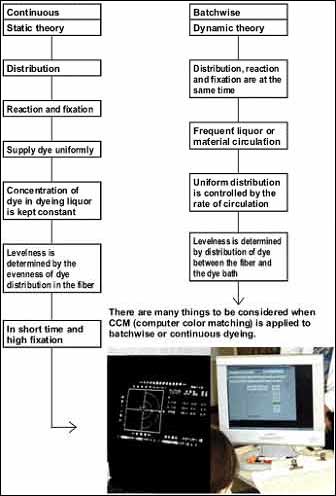
Home
Profile
Product
Range
Industries
Infrastructure
Our
Quality
Custom
Manufacturing
Network
Contact
Us
Send
Enquiry